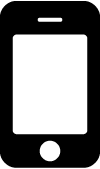
轴承是不可缺少的机器零件,限制运动并减小移动零件之间的摩擦力。
在制造轴承的过程中涉及多种磨削操作,包括端面磨削。由于该工艺涉及较大的接触面积,因此,具有良好导热性的耐磨磨料(如立方氮化硼 (CBN))是最合适的材料。磨料钝化会扩大接触面积,并提高工件受到热损伤的可能性。
元素六 ABN200 是这种应用的最佳选择,因其具有自磨锐功能——延长刀具使用寿命并降低工件受到热损伤的可能性。
恒速 (CV) 万向节一般与驱动轴末端连接,在不同的角度上传递旋转动力。恒速万向节可以让车轮在压过隆起物时进行有效的垂直移动,并同时传递动力。
由多晶立方氮化硼 (PCBN) 材料制成的刀具具有最高的工艺可靠性,并能在恒速万向节的硬加工中提供一致的高质量和准确度。元素六开发了 DBS900,这是一种性能非常高的牌号,可提供具有成本效益的工具解决方案。
传动轴对于将发动机动力和扭矩高效传递到汽车从动轮来说至关重要。车轮一般与连接在发动机上的变速箱相隔一段距离,因此传递动力的方法很重要。需要一种能够抵抗扭转和剪切应力的硬质材料——一般使用表面硬化钢以获得较长的组件使用寿命。
最好在硬化状态下加工这些零件,以避免在热处理工艺中变形。多晶氮化硼 (PCBN) 是用于实现硬零件车削的技术。
齿圈由环形硬化钢圈切削而成;它是汽车差速器中的一个大齿轮,由螺旋桨轴小齿轮驱动以将动力传递到驱动轴。
这些组件的理想材料是表面硬化钢。最好在硬化状态下加工这些零件,以避免在热处理工艺中变形。多晶立方氮化硼 (PCBN) 是用于实现硬零件车削的技术。针对此应用推荐元素六PureCut产品系列。DHA650是针对较少断续加工的理想选择。这两个牌号也可作为整体的插入式刀头,在加工基底材料刃口时逐步减少成本。
小齿轮是一种圆形硬化钢齿轮;它是与齿圈以一定的角度啮合,通过差速器将动力传递到驱动轴的小齿轮。
这些组件的理想材料是表面硬化钢。最好在硬化状态下加工这些零件,以避免在热处理工艺中变形。多晶立方氮化硼 (PCBN) 是用于实现硬零件车削的技术。
针对此应用推荐元素六PureCut产品系列。DHA650是针对较少断续加工的理想选择。这两个牌号也可作为整体的插入式刀头,在加工基底材料刃口时逐步减少成本。
凸轮轴可用于操作内燃机的进气阀和排气阀。由于曲轴和凸轮轴相对旋转之间的密切联系,需要对凸轮轴和凸轮凸角进行较严公差磨削。
立方氮化硼 (CBN) 是最适合磨削凸轮轴的磨料。不过,必须选择正确的颗粒形状以应对凸轮凸角外径上材料去除率的快速改变。ABN800 和 ABN900 是适合这种颇具挑战性的磨削操作的最佳颗粒类型。
发动机汽缸体或曲轴箱,包含数百个零件,占发动机总重量的 20 - 25%。一般使用铝合金铸造,需要大量精加工操作,如钻削、铰孔和攻丝。
多晶金刚石 (PCD) 切削刀具材料能够完成所有这些操作,为高产量生产线提供灵活有效的解决方案。
PCD 的超高硬度为切削刀具提供出色的耐磨性,比硬质合金刀具的加工速度要快。通过减少刀具更换次数、缩短生产停机时间和加快操作速度,带来显著的经济效益。
元素六的 PCD 金属牌号在铣削等断续切削操作以及铰孔等连续操作中提供更长的刀具使用寿命。
发动机汽缸体或曲轴箱,包含数百个零件,占发动机总重量的 20 - 25%。一般使用铝合金铸造,需要大量精加工操作,如端面铣削、凹面铣削和镗孔。
多晶金刚石 (PCD) 切削刀具材料能够完成所有这些操作,为高产量生产线提供灵活有效的解决方案。
PCD 的超高硬度为切削刀具提供出色的耐磨性,比硬质合金刀具的加工速度要快。通过减少刀具更换次数、缩短生产停机时间和加快操作速度,带来显著的经济效益。
元素六的 PCD 金属牌号在铣削等断续切削操作以及铰孔等连续操作中提供更长的刀具使用寿命。
曲轴是一种硬化钢轴,可以将活塞的往复运动转换为旋转运动,用于驱动变速箱和车轮。
由于旋转速度很快,曲轴必须被磨削至具有较高公差,以减少不必要的振动。
元素六立方氮化硼 (CBN) 产品,如 ABN800,相比传统粗砂岩,在曲轴磨削方面具备巨大优势。
汽车行业越来越注重效率增益,在发动机的功率重量增益上煞费苦心。
相比铸铁,铝合金具有显著的重量优势以及更高的导热系数。汽缸内径中仍需要耐磨涂层,技术已经发展进步,一般允许涂敷 0.2 - 0.3mm 厚的铁基涂层。此涂层随后会被加工至所需的厚度。
在之前采用昂贵的珩磨工艺进行这种加工的应用中,元素六的 PCBN 材料提供一种更加经济的方案,使用规定的刃口切削工具钻削衬套。这让最终用户获益于更快的加工时间、利用生产线上更廉价的机器和更加可控的工艺。
阀门用于大多数活塞发动机,以打开和关闭汽缸盖中的进气口和排气口。
立方氮化硼 (CBN) 是最适合用于磨削阀的磨料,这种阀门一般由镍铬合金钢制成。
在磨削工艺中使用电镀刀具可实现较高的材料去除率和生产率。元素六 ABN900 是理想之选,兼具统一的形状和良好的胎体把持力,从而提供经过改进的磨削工艺。其受控分解可产生更小的力,实现更高的材料去除率,同时磨料的耐磨性可实现较长的磨削时间和高生产率。
阀座是排气阀在关闭时受到支撑的表面。
采用粉末冶金 (PM) 材料制造,执行不同的操作,在阀座中产生圆锥形截面。由于 粉末冶金材料 很难加工,多晶立方氮化硼 (PCBN) 刀具是最适合阀座加工的材料。
由于粉末冶金材料种类繁多,适合既定应用的最佳 PCBN 牌号选择只能在材料分析后进行。
在车轮中首次使用铝和/或镁合金这一创举出现在 20 世纪 20 年代的赛车场上,现在这两种材料作为重要的造型元素应用于普通市场。它还有额外的性能优势,即重量减少,以及相对于冲压钢质车轮具有更好的刚性。
这些合金一般会铸造成一个整体,为设计人员提供更大的自由度。这些近净成形的铸件需要精加工为指定的大小和形状——通过铣削、钻削和车削操作。
多晶金刚石 (PCD) 应用广泛,主要得益于其刀具使用寿命长,在批量生产中提供显著的经济效益。最新的造型元件,如“金刚石切割轮”,利用 PCD 出色的切削刃质量来产生出色的表面光洁度,无需二次抛光操作。
CMX850 提供一种坚固而经济的解决方案,提高刀具制造商的加工能力,并为最终用户带来出众的切削性能。
制动盘使用卡钳将一对摩擦片挤压在制动盘上,以产生摩擦力,阻止车轴旋转,以降低速度或使其停止。
灰铸铁相对便宜并且容易生产。在 400°到 600°C 的温度下具有出色的导热性和稳定性。
利用多晶立方氮化硼 (PCBN),灰铸铁的可加工性得到大幅提升,可实现的高速在刀具上产生保护层,从而延长刀具使用寿命。
在追求更高车辆效率的过程中,减少重量是一个关键问题。之前,为了方便制造,典型的悬挂组件由冲压钢板制成,但整个行业目前正朝着冲压、铸造或加工铝材的方向发展。
元素六可以提供各种大直径、高产量的多晶金刚石 (PCD) 牌号,适应相关的应用领域。Syndite 系列 PCD 为铝铣削、镗孔和钻削提供性能最出色的选件。
在追求更高车辆效率的过程中,减少重量是一个关键问题。之前,为了方便制造,典型的悬挂组件由冲压钢板制成,但整个行业目前正朝着冲压、铸造或加工铝材的方向发展。
元素六可以提供各种大直径、高产量的多晶金刚石 (PCD) 牌号,适应相关的应用领域。Syndite 系列 PCD 为铝铣削、镗孔和钻削提供性能最出色的选件。
钢丝线、钢珠和钢带是轮胎的主要组件,可以将轮胎固定在轮辋上。它们提供轮胎的强度并最大化轮胎与道路的接触面。
拉线是一种金属加工工艺,可拉动线束穿过单个或一系列拉丝模,以减少线束横截面积。有多种拉线应用,包括电气接线和电缆。
单晶金刚石拉丝模提供出色的耐磨性并减少孔磨损变形,还可以缩短停机时间、提高生产率以及高质量拉制线材光洁度。
一般来说,轴承可用于汽车的多个应用领域,多种旋转轴都需要精确控制和移动。轴承材料需要高硬度、低摩擦系数和良好的热稳定性。
金刚石具备这三种属性且表现出卓越的性能,使轴承在其使用寿命期间运行时保持高公差尺寸。金刚石轴承会显著延长组件使用寿命,因为轴承表面是最先磨损的区域之一。
到目前为止,由于难以生产具备所需形状和尺寸的金刚石,还没有实现这种技术。元素六走在汽车行业金刚石轴承创新的前沿。
混合动力及电动汽车将继续增长和发展,加快传动系统组件的电气化——从电机和变速箱到燃油喷射、发动机和爆震控制。
在其中一些电子系统中,散热器在防止设备过热和发生故障方面具有至关重要的作用。例如,混合动力传动系统中的逆变器在将电池中的直流电转换为交流电,以驱动电机的过程中会产生大量热量。
在所有材料中,金刚石具有最高的室温导热性。它还具有电绝缘特性、高机械强度、重量轻和化学惰性——使其成为要求严苛的车辆传动系统环境中高压功率器件的首选材料。
未来的汽车会有更多嵌入式传感器,以监控动力传动系统的性能,无论是燃烧系统、电气系统还是混合动力系统都是如此。汽车传感器需要简单、低成本且非常可靠。
电化学传感器可用于控制和监控电池及燃料电池的性能。现代内燃机依靠传感器来管理燃烧。目前需要专业外部仪器进行的测量可以在车辆中进行,使用新的电化学传感器来监测排放。
金刚石是一种半导体,可以掺入硼来使其具有类似于金属的导电性,同时保持金刚石的惰性、坚固等特性。金刚石电极的稳定性、范围和灵敏度,有助于开发出新型简易电化学传感器。
可以在不同波长使用的多重成像系统能够增强驾驶员安全辅助功能。红外夜视等多光谱成像和毫米波成像(在机场扫描仪中使用)可显著增强能见度较低情况下的安全性。
金刚石是一种无与伦比的多光谱光学材料,具有从深紫外到可见、红外和毫米波段的窗口。这也是一种非常坚固的材料,十分适合作为防护窗。未来精密的多光谱传感器技术可以部署在多光谱金刚石精密光学元件后面,在汽车使用寿命期间防止其受到环境影响。
铝被应用于商用车的整个底盘结构部件,以减少簧上重量。更高效率和更高性能已然成为一种发展趋势,其应用范围会越来越广。轮毂架、直立悬架臂、控制臂和车轮等位置使用更轻的铝制部件可以使其更容易被底盘和减震器控制——提高性能并有助于提升整体经济性。
多晶金刚石 (PCD) 在高硅含量铝合金中表现出无与伦比的切削刀具性能。元素六可以提供各种适合复杂几何图形刀具的大直径、高产量的 PCD 牌号,适应相关的应用领域。Syndite 系列 PCD 为铝铣削、镗孔和钻削提供性能最出色的选件。
理想的制动盘应当轻巧且具有高耐磨性、高抗压强度和良好的导热性,这样才能减少车辆重量并提高整体性能。金属基复合材料 (MMC) 符合这些要求。这些材料一般使用铝合金作为基体,硬相材料作为强化组件,两者结合。
但是,MMC 难以有效地加工。多晶金刚石 (PCD) 是少数几种能够在车削和钻削应用中提供 MMC 经济切削性能的切削刀具材料。在碳化钨只能提供几分钟刀具使用寿命的应用中,PCD 可使用数小时。
凭借适用于车削应用的 Syndite 系列盘和适用于钻削的 Aero-Dianamics 圆形刀具,元素六提供解决 MMC 材料加工操作难题的最佳解决方案。
理想的制动盘应当轻巧且具有高耐磨性、高抗压强度和良好的导热性,这样才能减少车辆重量并提高整体性能。金属基复合材料 (MMC) 符合这些要求。这些材料一般使用铝合金作为基体,硬相材料作为强化组件,两者结合。
但是 MMC 难以有效地加工。多晶金刚石 (PCD) 是少数几种能够在车削和钻削应用中提供 MMC 经济切削性能的切削刀具材料。在碳化钨只能提供几分钟刀具使用寿命的应用中,PCD 可使用数小时。
凭借适用于车削应用的 Syndite 系列盘和适用于钻削的 Aero-Dianamics 圆形刀具,元素六提供解决 MMC 材料加工操作难题的最佳解决方案。