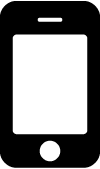
ベアリングは、可動部品間の動きの抑制と摩擦低減のために必要不可欠な機械部品です。
ベアリングの製造には、正面研削を含む多数の研削工程が存在します。接触面積が大きい工程のため、立方晶窒化ホウ素(CBN)など、良好な熱伝導性と耐摩耗性の高い砥粒製品が最適です。砥粒が摩耗して接触面積が増大すると、ワークに対する熱損傷の可能性が高まります。
エレメントシックスのABN200は切れ刃が自生するため、このアプリケーションに最適です。工具寿命を向上させ、ワークに対する熱損傷を低減します。
等速(CV)ジョイントは、通常ドライブシャフトに接続して取り付けられ、角度可変構造を通して回転と動力を伝達します。CVジョイントは、均一でない道の走行時に生じるホイールの有効な上下運動を許容しつつ動力を伝達します。
立方晶窒化ホウ素焼結体(PCBN)を使用した工具は、CVジョイントの硬質部品加工において、最大限の加工安定性と一貫した高い品質と精度を達成します。エレメントシックスは、コスト効果に優れた工具ソリューションとして、非常に高い性能グレードのDBS900を開発しました。
ドライブシャフトは、自動車の駆動輪にエンジンの馬力とトルクを効率的に伝達する上で不可欠な部品です。ホイールは通常エンジンと隣り合うギヤボックスから一定の距離に位置するため、動力伝達の手段は非常に重要となります。ねじれと剪断応力に耐える剛性をもつ硬質材が求められます。通常は、構成部品の長寿命化を図るため、肌焼鋼が使用されます。
熱処理工程中における変形を避けるために、部品の加工は硬化処理後に行うことが理想的です。立方晶窒化ホウ素焼結体(PCBN)は、高硬度材の旋削を可能にします。
リングギヤとは、リング状の焼入鋼に歯をきざんだ部品で、回転車軸に動力を伝達するプロペラシャフトピニオンによって駆動する、自動車のデファレンシャルに含まれる大型のギヤです。
これらの構成部品に適した材料は肌焼鋼です。熱処理工程中における変形を避けるために、部品の加工は硬化処理後に行うことが理想的です。立方晶窒化ホウ素焼結体(PCBN)は、高硬度材の旋削を可能にしました。
エレメントシックスのPureCut製品群はこのアプリケーションに推奨されるグレードです。断続加工が少ないオペレーションではDIA500をお勧めします。より断続加工が多い場合はDHA650が理想的な素材です。両グレード共にソリッドのインサートとしても提供可能で、超鋼裏付きのPCBN製品と比較し、エッジ当たりの大幅なコスト削減が可能です。
ピニオンとは、円形の焼入鋼製のギアで、ディファレンシャルを通して回転車軸に動力を伝達するために一定の角度でリングギヤとかみ合う小型のギヤです。
これらの構成部品に適した材料は肌焼鋼です。熱処理工程中における変形を避けるために、部品の加工は硬化処理後に行うことが理想的です。立方晶窒化ホウ素焼結体(PCBN)は、高硬度材の旋削を可能にしました。
エレメントシックスのPureCut製品群DHA650は、工具寿命を業界標準よりも50%以上向上させ、また、生産性向上を可能にするような高速加工を行うことも可能なため、このアプリケーションに推奨されるグレードです。DHA650はソリッドのインサートとしても提供可能で、超鋼裏付きのPCBN製品と比較し、エッジ当たりの大幅なコスト削減が可能です。
カムシャフトは、内燃エンジンの吸気・排気バルブを駆動するために用いられます。クランクシャフトとカムシャフトの相対回転は密接な関係にあるため、カムシャフトとカムローブの研削には厳しい公差が求められます。
立方晶窒化ホウ素(CBN)は、カムシャフトの研削に最適な研磨材です。ただし、カムローブ外径に対する急激な材料除去率の変化に対応できるよう、正確な粒形の選択を行う必要があります。ABN800とABN900は、課題の多いこの研削工程に最適な粒子タイプです。
エンジンシリンダーブロック、またはクランクケースは、多くの部品で構成されており、エンジン総重量の20~25%を占めます。通常アルミニウム合金を用いて鋳造され、正面フライス切削、ポケット加工、中ぐりなど多くの機械加工が必要となります。
ダイヤモンド焼結体(PCD)切削工具材料は、これらのすべての工程で使用することが可能で、量産ライン向けに柔軟で効率的なソリューションを提供します。
PCDの非常に高い硬度により、切削工具に非常に高い耐摩耗性を与えることができるため、超硬工具に比べてより高速な加工が可能となります。これにより、工具交換頻度と生産ラインダウンタイムの削減、スピードの実現により、多大な経済的メリットがもたらされます。
エレメントシックスのPCDメタルグレードでは、フライス加工などの断続切削加工、リーマ仕上げなどの連続加工の両方で長寿命の工具の製作が可能です。
エンジンシリンダーブロック、またはクランクケースは、多くの部品で構成されており、エンジン総重量の20~25%を占めます。通常アルミニウム合金を用いて鋳造され、正面フライス切削、ポケット加工、中ぐりなど多くの機械加工が必要となります。
ダイヤモンド焼結体(PCD)切削工具材料は、これらのすべての工程で使用することが可能で、量産ライン向けに柔軟で効率的なソリューションを提供します。
PCDの非常に高い硬度により、切削工具に非常に高い耐摩耗性を与えることができるため、超硬工具に比べてより高速な加工が可能となります。これにより、工具交換頻度と生産ラインダウンタイムの削減、スピードの実現により、多大な経済的メリットがもたらされます。
エレメントシックスのPCDメタルグレードでは、フライス加工などの断続切削加工、リーマ仕上げなどの連続加工の両方で長寿命の工具の製作が可能です。
クランクシャフトは高硬度焼入鋼のシャフトで、ピストンの往復運動をギヤボックス、つまり自動車のホイールを駆動するための回転運動に変換します。
高速で回転するため、クランクシャフトは不要な振動を低減するために厳しい公差で研削を行う必要があります。
ABN800を含むエレメントシックスの立方晶窒化ホウ素(CBN)製品群は、クランクシャフトの研削に用いられる従来砥粒製品よりもはるかに優れたメリットを提供します。
自動車産業での効率性の追求が高まるにつれて、エンジンの重量比出力の改善に多大な労力が注がれるようになっています。
アルミニウム合金は、鋳鉄に比べて重量の点で大幅に有利な上、より高い熱伝導性を有しています。現在でもシリンダーボア内面には耐摩耗コーティングが必要であり、技術の進歩により通常厚さ約0.2~0.3mmの鉄系コーティングが可能となりました。その後、所定の厚さになるようコーティング部分に機械加工が施されます。
以前はコストのかかるホーニング加工が施されていましたが、エレメントシックスのPCBN材料では、精密な刃先を持つ切削工具によるライナーのボアリングという経済的な選択が可能です。これは、加工時間の短縮、製造ライン内の安価な機械の活用、工程の制御改善などのメリットをエンドユーザーにもたらします。
バルブは、多くのピストンエンジンで使用され、シリンダーヘッドの吸気・排気ポートの開閉を行います。
立方晶窒化ホウ素(CBN)は、一般にニッケルクロム合金が用いられるバルブの研削に最適な研磨材料です。
研削工程に電着工具を使用することにより、材料除去率と生産性の向上が可能です。均一な形状と良好なボンド内保持力を併せ持つエレメントシックスのABN900は、研削工程の改善に寄与する最適な選択肢です。砥粒の破砕コントロールにより研削抵抗の抑制と高い材料除去率を達成すると同時に、砥粒の耐摩耗性により工具寿命の向上と生産性向上が可能となります。
バルブシートは、排気バルブが閉じる際にバルブが接触する面です。
バルブシートの材料は粉末金属(PM)であり、様々な工程により円錐の断面形状をしたバルブシートが形成されます。PMは機械加工が困難なため、バルブシートの加工には立方晶窒化ホウ素焼結体(PCBN)を使用した工具が最適です。
多様なPM素材が存在するため、特定のアプリケーションに最適なPCBNグレードの選定は材料の分析後に行われます。
ホイールへのアルミニウム合金、マグネシウム合金の使用は、1920年代のモータースポーツ用途が起源で、現在は重要なスタイリングの要素として市場一般で使用されています。プレス製スチールホイールと比較し、重量削減や高剛性という性能面でのメリットも提供します。
アロイホイールは通常ワンピースとして鋳造され、より大きな自由を設計者に提供します。ニアネットシェイプ鋳造では、フライスや穴あけ、旋盤加工などの工程により、所定のサイズや形状に仕上げる必要があります。
多結晶ダイヤモンド(PCD)は、主として大量生産における卓越した経済的メリットをもたらす工具の寿命延長の目的で、広範囲にわたり使用されています。「ダイヤモンドカットホイール」など最新のスタイル要素では、PDCの優れた切削エッジの品質を利用して、二次研磨工程を経ることなく驚異的な表面仕上げが可能です。
CMX850は、工具メーカーには加工性の向上を、エンドユーザーには特筆すべき切削能力をもたらす、堅牢で経済的なソリューションです。
ディスクブレーキは、キャリパーを用いて一組のパッドをディスクに押し付けることにより、車軸の回転を低減または停止するために必要な摩擦力を生み出します。
ねずみ鋳鉄は比較的安価で製造が容易です。400°Cから600°Cの温度下で優れた熱伝導性と熱安定性を発揮します。
ねずみ鋳鉄の加工性は、立方晶窒化ホウ素焼結体(PCBN)の使用により劇的に向上します。高速加工により保護膜が生成され、工具の寿命を飛躍的に延長させることができます。
重量削減は、自動車の効率向上において重要な問題です。これまでサスペンション構成部品には、製造が容易なためにプレス鋼が使用されてきましたが、業界ではプレス、鋳造アルミニウム、アルミ加工品へと移行しています。
エレメントシックスは、このアプリケーションに適合する大型ディスク形状で歩留まりも高い、幅広い形状のダイヤモンド焼結体グレード(PCD)を取り揃えています。PCDのシンダイト製品群は、アルミニウムのフライス、中ぐり、穴あけ加工のための最高の性能オプションを提供します。
重量削減は、自動車の効率向上において重要な問題です。これまでサスペンション構成部品には、製造が容易なためにプレス鋼が使用されてきましたが、業界ではプレス、鋳造アルミニウム、アルミ加工品へと移行しています。
エレメントシックスは、このアプリケーションに適合する大型ディスク形状で歩留まりも高い、幅広い形状のダイヤモンド焼結体グレード(PCD)を取り揃えています。PCDのシンダイト製品群は、アルミニウムのフライス、中ぐり、穴あけ加工のための最高の性能オプションを提供します。
鋼製ワイヤコード、ビーズ、ベルトは、タイヤの重要な構成部品であり、ホイールのリムにタイヤを固定する役割を果たします。タイヤに強度を付与し、タイヤと路面の接地面を最大化します。
線引き加工とは、ワイヤを1つもしくは複数のダイスの間で引き抜くことにより、ワイヤの断面積を縮小する金属加工法です。電線やケーブルなど、線引き加工には数多くのアプリケーションがあります。
単結晶ダイヤモンドワイヤ線引きダイスは、卓越した耐摩耗性を持ち、偏摩耗による穴の歪みを低減させるため、ダウンタイムの削減、高生産性、線引きワイヤの高品質な仕上げが可能となります。
ベアリングは自動車の多くのアプリケーションで広く使用されており、複数の回転軸では精密な制御と動きが要求されます。ベアリング材料には、高硬度、低摩擦係数、良好な熱安定性が要求されます。
ダイヤモンドは、この3つの特性すべてにおいて驚異的な性能を発揮し、ベアリングの寿命にわたり厳しい公差を維持することが可能です。ベアリングの表面は最初に摩耗する部分の1つであるため、ダイヤモンドベアリングは構成部品の寿命を飛躍的に伸ばす可能性があります。
現在の時点では、必要な形状やサイズのダイヤモンド製造が困難なため、これは実現していません。エレメントシックスは、自動車産業用ダイアモンドベアリングのイノベーションの最先端を担っています。
ハイブリッド自動車、電気自動車の増加と開発は継続することが予測され、モーター、トランスミッションをはじめ、燃料噴射装置やエンジン、さらにノッキングの制御にいたるまで、ドライブトレイン構成部品の電化が進行します。
これらの電子系統の一部では、装置の過熱と故障を防ぐためにヒートスプレッダが不可欠です。例えば、ハイブリッドドライブトレイン内のインバーターでは、モーターを駆動するためにバッテリーからの直流電流を交流電流に変換する際、多量の熱が発生します。
ダイヤモンドは、あらゆる素材の中でも常温下における熱伝導性が最も高い素材です。高い機械的強度と電気的絶縁性を兼ね備え、軽量であり化学的に不活性であるため、自動車ドライブトレインという過酷な環境下における高電圧パワーデバイスのための材料に最適です。
未来の自動車には、内燃、電気、ハイブリッドシステムであるかに関わらず、パワートレインを監視するためにより多くのセンサーが組み込まれることが予測されます。自動車用センサーには、シンプルで低価格であることに加え、高い信頼性が求められます。
電気化学センサーは、バッテリーと燃料電池の性能の制御と監視に使用できます。現代の内燃エンジンは、燃焼管理をセンサーに依存しています。排気の監視に新しい電気化学センサーを使用すれば、現在特殊な外部装置を必要とする測定を自動車内で行える可能性があります。
ダイヤモンドは半導体であり、ホウ素をドープすると、ダイヤモンドの不活性で堅牢な特性を維持しつつ、金属のような電気的伝導性を付与することができます。ダイヤモンド電極は、安定性、範囲、感度を持たせて製造できるため、新しいタイプのシンプルな電気化学センサーの開発が可能です。
異なる波長で作動する複数のイメージングシステムは、運転者の安全を補助する機能を強化することができます。赤外線ナイトビジョンやミリ波イメージング(空港でのスキャナーなどに使用)のマルチスペクトルイメージングは、悪視界下における安全性を大幅に高めます。
ダイヤモンドは、マルチスペクトル光学用として比類のない素材であり、光学窓がカバーする波長域は深紫外線から可視光線、赤外線、ミリ波まで及びます。また堅固な素材であるため、保護窓としての役割も果たします。マルチスペクトルダイヤモンド精密光学素材と併せて未来の繊細なマルチスペクトルセンサー技術を使用すれば、自動車のライフサイクルにわたり環境からセンサーを保護することができます。
アルミニウムは、ばね上重量を軽減するため、市販自動車のシャーシ全体に構造部材として既に使用されています。優れた効率と性能改善に対する要求が高まるにつれて、アルミニウムの使用量はさらに増加することが予測されます。ハブキャリア、アップライトサスペンションアーム、コントロールアーム、ホイールなどに軽量アルミニウム部材を使用した場合、シャシーやショックアブソーバによる制御が容易となり、性能と全体的な経済性が改善します。
多結晶ダイヤモンド焼結体(PCD)は、高シリコン含有アルミニウム合金用切削工具として比類のない性能を発揮します。エレメントシックスは、このアプリケーションに適合する複雑形状の工具製造のための大型ディスク、高歩留まりの形状の幅広いPCDグレードを取り揃えています。PCDのシンダイト製品群は、アルミニウムのフライス、中ぐり、穴あけ加工のための最高の性能オプションを提供します。
理想的なブレーキディスクには、車両重量の削減と全体のパフォーマンス向上のため、軽量で高い耐摩耗性と圧縮強度、そして良好な熱伝導性が期待されます。金属複合材料(MMC)は、これらすべての要求を満たします。典型的な金属系複合材は、アルミニウム合金を基材とし、補強部材として硬質層の素材が組み合わされています。
しかしながらMMCは、効率的な加工が非常に難しい素材です。多結晶ダイヤモンド焼結体(PCD)は、MMCの旋削、穴あけ加工を経済的に実施できる限られた切削工具材の1つです。超硬工具ではわずか数分の工具寿命に対し、PCDは何時間もの作業が可能です。
エレメントシックスは、旋削アプリケーション用シンダイトディスク、穴あけ用エアロダイアナミクス回転工具素材など、MMCの機械加工の課題に対応するための最適なソリューションを提供します。
理想的なブレーキディスクには、車両重量の削減と全体のパフォーマンス向上のため、軽量で高い耐摩耗性と圧縮強度、そして良好な熱伝導性が期待されます。金属系複合材料(MMC)は、これらすべての要求を満たします。典型的な金属系複合材には、アルミニウム合金を基材とし、補強部材として硬質層の素材が組み合わされています。
しかしながらMMCは、効率的な加工が非常に難しい素材です。多結晶ダイヤモンド焼結体(PCD)は、MMCの旋削、穴あけ加工を経済的に実施できる限られた切削工具材の1つです。超硬工具ではわずか数分の工具寿命に対し、PCDは何時間もの作業が可能です。
エレメントシックスは、旋削アプリケーション用シンダイトディスク、穴あけ用エアロダイアナミクス回転工具素材など、MMCの機械加工の課題に対応するための最適なソリューションを提供します。